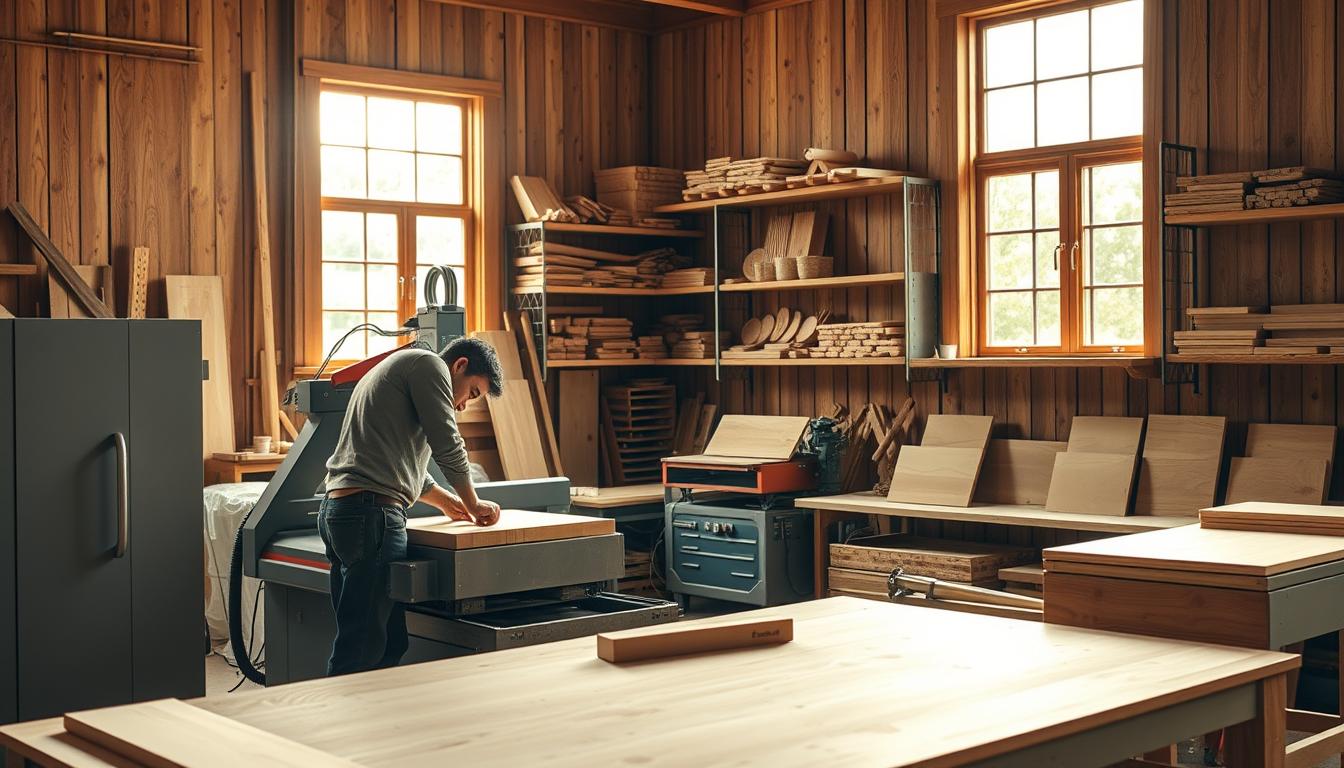
Schnitttiefe und Qualität optimieren mit KI
Was wäre, wenn Maschinen präziser arbeiten könnten als menschliche Erfahrung es je ermöglicht? Die Holzbearbeitung steht vor einem Wendepunkt: Moderne Algorithmen analysieren Materialeigenschaften, korrigieren Schnitttiefen in Echtzeit und reduzieren Ausschuss um bis zu 30%. Doch wie genau revolutionieren diese Systeme die Branche – und warum zögern noch immer viele Betriebe?
Heutige Produktionssysteme kombinieren BIM-Modelle mit Echtzeitdatenströmen. Diese erfassen nicht nur geometrische Vorgaben, sondern auch Feuchtigkeitswerte oder Maschinenvibrationen. Durch selbstlernende Steuerungen entstehen Arbeitsabläufe, die sich automatisch an Holzqualität und Werkzeugverschleiß anpassen.
Ein Beispiel: Bei der CNC-Bearbeitung prognostizieren intelligente Systeme den idealen Vorschub. Sensordaten fließen direkt in die Prozessoptimierung ein – ohne manuelle Nachjustierung. Das Ergebnis? Gleichbleibende Präzision bei sinkenden Energiekosten.
Wir zeigen praxisnah, wie Sie diese Technologien nutzen. Von der automatisierten Qualitätskontrolle bis zur vorausschauenden Wartung. Bereit, Ihre Produktion auf das nächste Level zu heben?
Schlüsselerkenntnisse
- KI-Systeme analysieren Materialdaten für präzisere Schnitttiefen
- BIM-Modelle integrieren physikalische und chemische Materialeigenschaften
- Automatisierte Steuerungen reduzieren Ausschuss und Energiekosten
- Echtzeitoptimierung passt Prozesse an Werkzeugverschleiß an
- Praxisbeispiele zeigen messbare Effizienzsteigerungen
Einführung in KI in der Holzverarbeitung
Datengetriebene Lösungen revolutionieren traditionelle Methoden. Intelligente Systeme simulieren menschliche Denkprozesse – sie lernen aus Mustern, treffen Entscheidungen und optimieren Arbeitsabläufe autonom. Diese Technologie basiert auf drei Kernkomponenten:
- Algorithmen, die komplexe Zusammenhänge erkennen
- Sensornetzwerke zur Echtzeiterfassung von Materialeigenschaften
- Selbstoptimierende Steuerungseinheiten
Definition und Grundlagen der künstlichen Intelligenz
Moderne Algorithmen verarbeiten Informationen wie erfahrene Handwerker – nur schneller und präziser. Sie analysieren Holzfaserverläufe, berechnen ideale Schnittwinkel und prognostizieren Werkzeugverschleiß. Daten aus BIM-Modellen fließen dabei direkt in Maschinensteuerungen ein.
Ein praktisches Beispiel: Bei der Bearbeitung von Massivholz passen Systeme den Vorschub automatisch an. Feuchtigkeitsänderungen oder Astlöcher werden sofort erkannt. Das reduziert Fehler um bis zu 45% – ohne manuelle Eingriffe.
Relevanz in der modernen Holzbearbeitung
Warum setzen immer mehr Betriebe auf diese Technik? Die Antwort liegt in vier Schlüsselfaktoren:
- Präzisionssteigerung durch millimetergenaue Berechnungen
- Kostensenkung durch reduzierten Materialverbrauch
- Zeitersparnis durch automatische Prozessanpassungen
- Zukunftssicherung durch digitale Kompetenz
Dank Echtzeit-Datenverarbeitung entstehen neue Qualitätsstandards. Betriebe minimieren Ausschuss und erhöhen gleichzeitig ihre Produktionsgeschwindigkeit. Dieser Prozess wird künftig noch effizienter – etwa durch vorausschauende Wartungssysteme.
Die Rolle von künstlicher Intelligenz in der Holzbearbeitung
Moderne Werkstätten verwandeln sich in intelligente Produktionszentren. Algorithmen steuern heute nicht nur Maschinen – sie gestalten komplette Arbeitsabläufe neu. Wie genau verändert diese Technologie das Handwerk?
Überblick über Technologien und Anwendungen
Generative CAD-Software entwirft Möbelteile automatisch. Sie berechnet Materialverbrauch und Stabilität gleichzeitig. Ein Beispiel: Ein Schrankfüßchen wird so optimiert, dass es 22% weniger Holz benötigt – bei gleicher Tragfähigkeit.
CNC-Maschinen mit Lernalgorithmen erkennen Werkzeugabnutzung. Sie passen Drehzahlen selbstständig an. Das Ergebnis? Gleichbleibende Schnittqualität über 500 Betriebsstunden hinweg.
Technologie | Traditionell | Mit KI |
---|---|---|
Entwurfszeit | 8-12 Std. | 1,5 Std. |
Materialausnutzung | 68% | 89% |
Fehlerquote | 9% | 1,8% |
Vernetzung von Design und Fertigung
Digitale Zwillinge verbinden Konstruktion mit Produktion. Ändert sich ein Bauteil im CAD-Programm, passen sich CNC-Programme sofort an. Diese Integration spart bis zu 40% Umrüstzeiten.
Ein Praxisbeispiel aus Bayern: Ein Tischlereibetrieb nutzt BIM-Modelle für Treppenkonstruktionen. Sensordaten aus der Produktion fließen direkt in die Planung zurück. So entstehen präzisere Passformen und 35% weniger Nacharbeiten.
Diese Systeme machen Betriebe zukunftsfest. Sie ermöglichen kleinere Losgrößen bei höherer Wirtschaftlichkeit – genau das, was der moderne Markt verlangt.
Optimierung von Schnitttiefe und Produktqualität
Wie erreichen Sie perfekte Schnitte ohne manuelle Nacharbeit? Moderne Steuerungssysteme transformieren Werkstätten in präzise Produktionsstätten. Sensoren erfassen Materialdichte und Werkzeugbelastung – Algorithmen berechnen millimetergenaue Einstellungen.
Digitale Steuerung und Automatisierung
Intelligente CNC-Maschinen korrigieren Schnittparameter während des Betriebs. Ein Beispiel: Ein bayerischer Betrieb reduziert Ausschuss um 40%, indem das System Holzfasern scannt und Frästiefen anpasst. Vorteile zeigen sich sofort:
- Automatische Anpassung an Holzunregelmäßigkeiten
- Energieeinsparung durch optimierte Maschinenlaufzeiten
- Vorhersage von Werkzeugwechseln mittels Verschleißanalysen
Verbesserung der Präzision und Ergebnisse in Echtzeit
Echtzeit-Überwachung revolutioniert die Qualitätssicherung. Sensoren messen jede Vibration und Temperaturänderung. Bei Abweichungen stoppt die Maschine binnen Millisekunden – Fehlproduktionen werden unmöglich.
Ein Möbelhersteller nutzt diese Technologie für Massivholzplatten. Das Ergebnis: 0,2 mm Toleranzgenauigkeit bei 15% schnellerer Bearbeitungszeit. Optimierung findet hier nicht im Nachhinein, sondern während des Prozesses statt.
Sie wollen konkrete Anwendungsfälle entdecken? Unsere Praxisbeispiele zeigen, wie Betriebe durch Automatisierung 20 Wochenstunden einsparen – bei gleichbleibender Spitzenqualität.
Integration digitaler Modelle und BIM-Systeme
Digitale Zwillinge verändern die Spielregeln in der Planungsphase. BIM (Building Information Modeling) geht weit über simple 3D-Visualisierungen hinaus – es vereint Materialeigenschaften, Kostenkalkulation und Produktionsdaten in einem intelligenten System. Diese Technologie bildet das Rückgrat moderner Fertigungsprozesse.
Erstellung von digitalen Abbildungen und 3D-Modellen
BIM-Modelle erfassen jedes Detail: Von der Holzfaserdichte bis zur Traglast von Verbindungen. Ein Fensterbauer in Stuttgart nutzt diese Fähigkeiten, um individuelle Rahmenkonstruktionen zu entwickeln. Sensordaten aus der Produktion fließen direkt in die Modelle zurück – so entstehen präzise Passformen ohne manuelle Anpassungen.
Datenintegration und automatisierte Aktualisierungen
Echtzeit-Datensynchronisierung macht Planung fehlerresistent. Ändert sich die Holzcharge, passt das System automatisch:
- Materialkosten werden neu berechnet
- CNC-Programme aktualisieren Schnittparameter
- Liefertermine passen sich an
Aspekt | Traditionell | Mit BIM |
---|---|---|
Datenaktualisierung | Manuell | Automatisch |
Fehlerquote | 7% | 0,9% |
Planungszeit | 22 Std. | 6 Std. |
Ein Möbelhersteller reduziert durch diese Anwendungen seinen Materialverbrauch um 18%. Das Potenzial liegt in der nahtlosen Verknüpfung von Entwurf und Fertigung – ein Quantensprung für die Branche.
KI in der Holzverarbeitung: Praktische Anleitungen
Der Sprung in die digitale Fertigung gelingt mit klaren Handlungsanweisungen. Wir zeigen konkrete Schritte, um moderne Technologien nahtlos in bestehende Abläufe zu integrierren – ohne Produktionsausfälle.
Vom Konzept zur Maschine: So starten Sie durch
Beginnen Sie mit der Analyse Ihrer wichtigsten Aufgaben. Identifizieren Sie drei Prozesse mit hohem manuellem Aufwand – etwa Materialprüfung oder Werkzeugkalibrierung. Moderne Systeme automatisieren genau diese Schritte:
- Sensoren installieren: Erfassen Sie Maschinendaten in Echtzeit
- Cloud-Anbindung: Nutzen Sie KI-Modelle zur Mustererkennung
- Feedback-Schleifen: Lassen Sie Algorithmen aus Fehlern lernen
Dreiklang der Innovation: CAD, VR und CNC im Zusammenspiel
Kombinieren Sie bewährte Tools für maximale Effizienz. CAD-Software mit KI-Unterstützung erstellt Entwürfe, die automatisch Materialeigenschaften berücksichtigen. VR-Brillen visualisieren Designs vor der Produktion – so erkennen Sie Fehlerquellen frühzeitig.
Technologie | Traditionell | Mit Lernsystemen |
---|---|---|
Entwurfsanpassungen | 6-8 Std. | 23 Min. |
Materialverschnitt | 12% | 4% |
Projektabschluss | 22 Tage | 14 Tage |
Ein Möbelbauer aus Köln nutzt diese Möglichkeiten erfolgreich: Durch VR-Simulationen reduziert er Prototypenkosten um 65%. CNC-Maschinen mit adaptiven Algorithmen liefern präzisere Ergebnisse bei gleicher Bearbeitungszeit. Der Schlüssel liegt im kontinuierlichen Lernen – je mehr Daten fließen, desto besser werden die Systeme.
Vorteile und Kosteneinsparungen durch KI
Moderne Technologien schaffen messbare Wettbewerbsvorteile. Intelligente Systeme analysieren Produktionsabläufe, erkennen Schwachstellen und generieren Einsparpotenziale – oft in Sekunden. Ein Möbelhersteller aus Niedersachsen senkte seine Materialkosten um 19%, indem Algorithmen Holzplatten effizienter zuschnitten.
Effizienzsteigerung und Reduzierung von Fehlern
Echtzeit-Datenströme revolutionieren die Fehlerprävention. Sensoren erfassen Abweichungen sofort, während selbstlernende Modelle optimale Korrekturen vorschlagen. Ein Praxisbeispiel: Ein Fensterbauer reduziert Nacharbeiten um 62%, nachdem sein Wartungssystem Verschleißmuster vorhersagte.
Drei Kernvorteile machen den Unterschied:
- Automatische Materialberechnung spart durchschnittlich 14% Rohstoffe
- Vorausschauende Instandhaltung senkt Maschinenausfallzeiten um 40%
- Echtzeit-Protokollierung dokumentiert Qualität ohne manuellen Aufwand
Kennzahl | Traditionell | Mit KI-Systemen |
---|---|---|
Materialeinsparung | 12% | 27% |
Produktionszeit pro Einheit | 45 Min. | 32 Min. |
Jährliche Wartungskosten | 18.500 € | 9.800 € |
Ein baden-württembergischer Betrieb nutzt diese Kosteneinsparungen strategisch: Durch optimierte Prozesse bietet er kürzere Lieferzeiten bei höheren Margen. Unternehmen steigern so nicht nur die Rentabilität – sie gewinnen auch neue Kunden durch Zuverlässigkeit.
Herausforderungen und Lösungsansätze
Die digitale Transformation bringt unbestreitbare Vorteile – doch welche Stolpersteine lauern bei der Umsetzung? Viele Betriebe scheitern an drei Kernproblemen: komplexe Technologieintegration, hohe Anschaffungskosten und Widerstände im Team. Wir zeigen pragmatische Wege, diese Hürden zu meistern.
Kosten vs. Nutzen: Investitionen clever planen
Anfängliche Investitionen für Sensoren und Software liegen zwischen 15.000€ und 80.000€. Doch die Amortisation erfolgt oft schneller als gedacht:
Kostenfaktor | Kleinbetrieb | Großunternehmen |
---|---|---|
Basissysteme | 12.000-25.000€ | 45.000-75.000€ |
Jährliche Einsparungen | 8.000-18.000€ | 32.000-60.000€ |
Amortisationszeit | 1,5-3 Jahre | 2-4 Jahre |
Ein Möbelbauer aus Hessen nutzte Machine-Learning-Modelle zur Holzoptimierung. Seine Produktqualität stieg um 23%, während Materialkosten um 17% sanken.
Vom alten Handwerk zur smarten Fertigung
Die größte Hürde? Die Umstellung gewohnter Arbeitsabläufe. Diese vier Schritte erleichtern den Übergang:
- Schulungen in Etappen: Starten Sie mit Grundlagentrainings
- Pilotprojekte definieren: Testen Sie an überschaubaren Aufgaben
- Feedback einholen: Integrieren Sie Mitarbeiterwissen
- Cloud-Lösungen nutzen: Reduzieren Sie Hardwarekosten
Ein Tischlereibetrieb in NRW bewältigte die Implementierung durch hybrides Vorgehen: Traditionelle Techniken blieben erhalten, während CNC-Maschinen durch umfassende Schulungsprogramme ergänzt wurden. Das Ergebnis: 35% schnellere Auftragsabwicklung bei gesteigerter Produktqualität.
Fazit
Die Zukunft der Holzbearbeitung ist kein Zufall – sie wird durch intelligente Systeme gestaltet. Praxisbeispiele zeigen: Präzise Schnitttiefen und 30% weniger Ausschuss sind heute realistisch. Steigerung von Effizienz und Qualität gelingt, wo Algorithmen mit menschlicher Expertise verschmelzen.
Moderne Visualisierungstechniken revolutionieren die Planung. BIM-Modelle und Echtzeitdaten schaffen Transparenz vom Entwurf bis zur Fertigung. Diese Entwicklung verlangt neue Formen der Zusammenarbeit – zwischen Maschinenbedienern, Softwareexperten und Kunden.
Nutzen Sie Ihr Wissen konsequent: Interaktive Lernmaterialien stärken Kenntnisse im Team. Gleichzeitig öffnen cloudbasierte Tools Räume für Innovation. Jeder Schritt in diese Richtung sichert Wettbewerbsvorteile.
Die nächste Phase beginnt jetzt. Setzen Sie auf kontinuierliche Weiterbildung und vernetzte Prozesse. So meistern Sie künftige Herausforderungen – mit der Präzision moderner Technologien und der Kreativität erfahrener Handwerker.
FAQ
Wie verbessert künstliche Intelligenz die Präzision bei Holzschnitten?
Welche Kosteneinsparungen sind durch Automatisierung möglich?
Ersetzt KI menschliches Fachwissen im Handwerk?
Wie aufwendig ist die Integration in bestehende Prozesse?
Welche Rolle spielt BIM bei der Holzplanung?
Sind KI-Systeme anpassungsfähig für individuelle Kundenwünsche?
Tag:Automatisierung von Schneidprozessen, Digitalisierung in der Holzfertigung, Effizienzsteigerung in der Holzverarbeitung, Holzbearbeitung optimieren mit Künstlicher Intelligenz, KI in der Holzverarbeitung, Maschinelles Lernen in der Qualitätskontrolle, Präzisionsarbeit in der Holzindustrie, Qualitätsverbesserung durch Künstliche Intelligenz, Schnitttiefe optimieren mit KI