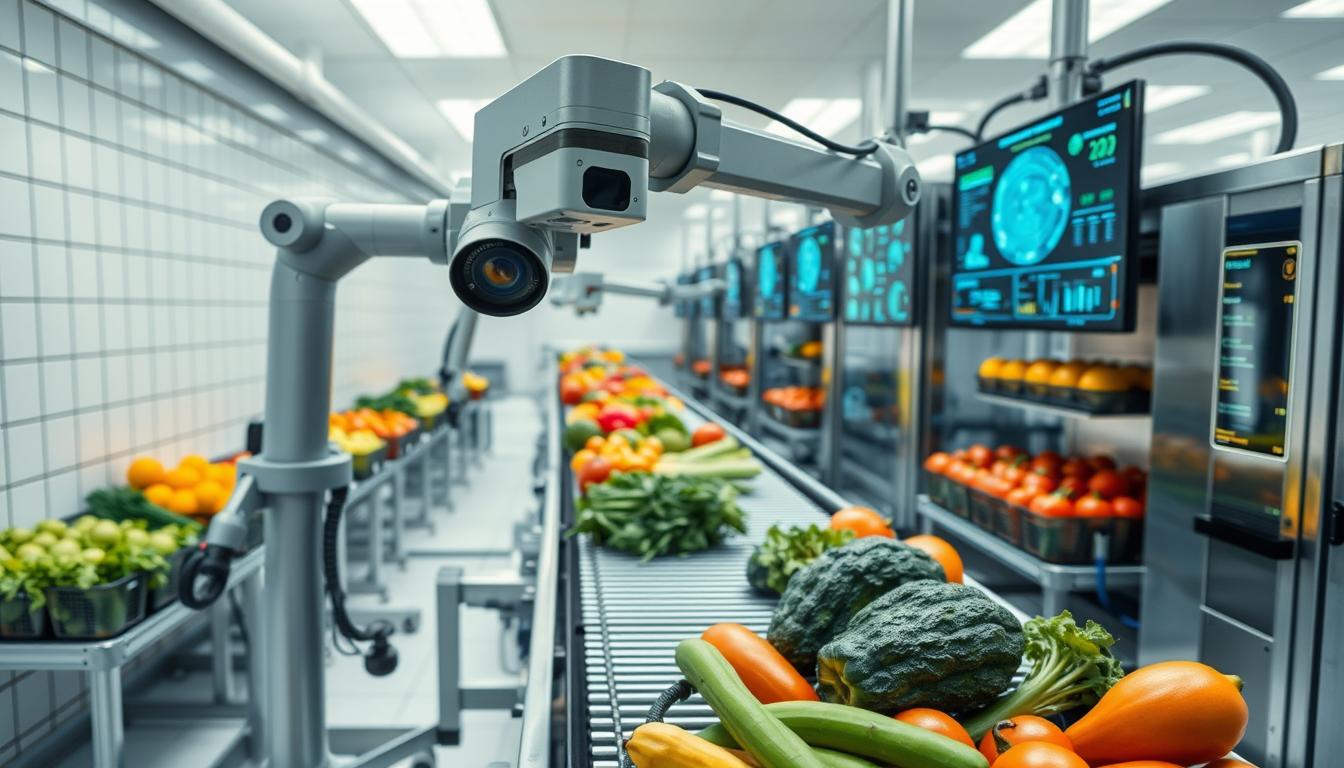
Qualität und Sicherheit automatisch prüfen
Was wäre, wenn Fehler in der Lebensmittelproduktion schon vor dem menschlichen Auge sichtbar würden? Intelligente Systeme analysieren heute Mikrometer-kleine Abweichungen oder chemische Unregelmäßigkeiten – und das in Echtzeit. Sie fragen sich, wie das möglich ist?
Moderne Technologien revolutionieren die Lebensmittelsicherheit, indem sie präzise Datenauswertung mit industrieller Praxis verbinden. Traditionelle Methoden stoßen an Grenzen, wenn es um Geschwindigkeit oder komplexe Mustererkennung geht. Hier setzen maschinelle Lernverfahren an: Sie identifizieren Risikofaktoren, bevor diese kritisch werden.
Die Vorteile liegen auf der Hand: Kontinuierliche Überwachung senkt Rückrufquoten. Automatisierte Prozesse reduzieren manuelle Fehlerquellen um bis zu 68% (Quelle: Industriestudien 2023). Gleichzeitig entstehen völlig neue Optimierungspotenziale – von der Rohstoffauswahl bis zur Logistik.
Wir zeigen Ihnen, warum die Kombination aus menschlicher Expertise und algorithmischer Präzision den Qualitätsstandard neu definiert. Denn Sicherheit ist kein Zufall, sondern das Ergebnis intelligenter Systeme.
Das Wichtigste in Kürze
- Algorithmen erkennen mikroskopische Qualitätsabweichungen in Millisekunden
- Echtzeitdaten ermöglichen proaktive Risikominimierung
- Traditionelle Kontrollmethoden werden durch prädiktive Analysen ergänzt
- Kosteneinsparungen durch reduzierte Ausschussquoten
- Skalierbare Lösungen für Betriebe jeder Größenordnung
Einleitung
Wie schaffen es moderne Betriebe, Sicherheit und Effizienz in der Lebensmittelbranche zu vereinen? Die Antwort liegt in der intelligenten Vernetzung von bewährten Methoden und digitalen Lösungen. Jede dritte Rückrufaktion ließe sich durch präventive Maßnahmen vermeiden – ein Potenzial, das heute mehr denn je genutzt werden muss.
Überblick zum Thema und Relevanz der Lebensmittelsicherheit
Globalisierung und komplexe Lieferketten erhöhen das Risiko von Qualitätsmängeln. Gleichzeitig wachsen die regulatorischen Anforderungen. Traditionelle Stichprobenkontrollen reichen nicht mehr aus, um lückenlose Sicherheit zu gewährleisten.
Hier setzen innovative Ansätze an: Die nahtlose Integration intelligenter Modelle in bestehende Prozesse ermöglicht Echtzeitanalysen. Sensoren erfassen Temperaturverläufe, Kamerasysteme erkennen Verpackungsfehler – und das rund um die Uhr.
Ziele des How-To Guides
Dieser Leitfaden zeigt Ihnen:
- Wie Sie technologische Lösungen schrittweise implementieren
- Welche Synergien zwischen manuellen Checks und automatisierten Systemen entstehen
- Wie Sie Ressourcen durch prädiktive Analysen optimieren
Unternehmen aller Größen profitieren von skalierbaren Ansätzen. Die Kombination aus menschlicher Expertise und maschineller Präzision schafft nachhaltige Wertschöpfungsketten. Wir begleiten Sie bei diesem Transformationsprozess – von der ersten Analyse bis zur vollständigen Integration.
Grundlagen der Lebensmittelkontrolle und Qualitätssicherung
Jede erfolgreiche Lebensmittelproduktion baut auf drei Säulen auf: präzise Standards, lückenlose Prozesse und kontinuierliche Verbesserung. Wir zeigen Ihnen, wie diese Elemente moderne Sicherheitskonzepte prägen – und warum sie heute intelligenter umgesetzt werden denn je.
Bedeutung von Hygiene, Normen und Produktqualität
Hygienevorschriften wie die ISO 22000 bilden das Fundament jeder Produktionskette. Doch wie entsteht daraus echte Sicherheit? Durch den Einsatz digitaler Protokolle, die kritische Parameter automatisch überwachen. Sensoren messen Luftfeuchtigkeit, Kameras analysieren Oberflächenstrukturen – in Echtzeit.
Einheitliche Qualitätsstandards reduzieren Risiken um bis zu 43% (Websource-Daten 2023). Lösungen wie HACCP-Systeme verbinden dabei menschliche Expertise mit maschineller Präzision.
Wichtige Kontrollprozesse in der Lebensmittelindustrie
Moderne Kontrollen folgen vier Schritten:
- Rohstoffprüfung mittels Spektralanalyse
- Produktionsüberwachung durch IoT-Sensoren
- Endkontrolle mit automatisierten Inspektionssystemen
- Dokumentation via Blockchain-Technologie
Vorausschauende Wartung spielt hier eine Schlüsselrolle: Algorithmen erkennen Maschinenabweichungen, bevor Störungen auftreten. Daten aus verschiedenen Quellen fließen zusammen und schaffen transparente Entscheidungsgrundlagen.
Darüber hinaus ermöglichen cloudbasierte Lösungen die Synchronisation globaler Lieferketten. So entsteht ein Netzwerk, das Sicherheit nicht begrenzt – sondern multipliziert.
Aktuelle Herausforderungen in der Lebensmittelkontrolle
Die Lebensmittelbranche steht vor einem technologischen Wendepunkt. Während herkömmliche Verfahren seit Jahrzehnten funktionieren, offenbaren sich heute systematische Schwachstellen. Globalisierte Lieferketten und strengere Verbrauchererwartungen erfordern neue Ansätze.
Traditionelle Methoden versus moderne Technologien
Manuelle Stichprobenprüfungen erfassen maximal 2-3% der Produktion. Zeitverzögerungen bei Laboranalysen führen zu kritischen Lücken in der Qualitätskontrolle. Moderne Systeme scannen dagegen 100% der Ware in Echtzeit – mit Algorithmen, die selbst Mikrometerfehler erkennen.
Ein Praxisbeispiel: Ein Molkereibetrieb reduzierte Rückrufaktionen um 71%, nachdem er automatisierte Inspektionslösungen implementierte. Solche Technologien überwinden die Grenzen visueller Kontrollen.
Regulatorische Anforderungen und praktische Probleme
EU-Verordnungen wie die VO (EG) Nr. 852/2004 verlangen lückenlose Dokumentation. Viele Betriebe kämpfen mit:
- Hohen Personalkosten für manuelle Datenerfassung
- Inkompatiblen IT-Strukturen zwischen Lieferanten
- Verzögerter Risikobewertung durch veraltete Systeme
Die Implementierung cloudbasierter Plattformen löst diese Herausforderungen. Sie ermöglicht synchronisierte Qualitätsstandards über gesamte Produktionsnetzwerke hinweg. Unternehmen, die diese Fähigkeit zur Digitalisierung nutzen, steigern ihre Marktanteile nachweislich schneller.
Laut einer aktuellen Studie sparen Betriebe durch moderne Systeme bis zu 23 Stunden wöchentlich bei der Dokumentation. Diese Effizienzgewinne machen den Unterschied im Wettbewerb.
KI bei Lebensmittelkontrolle: Technologien und Praxisanwendungen
Moderne Technologien verändern die Art, wie Qualität gesichert wird. Intelligente Systeme überwachen jeden Produktionsschritt – vom Rohstoff bis zum verpackten Produkt. Diese Lösungen kombinieren präzise Sensorik mit lernfähigen Algorithmen, die selbst kleinste Abweichungen erkennen.
Visuelle Prüfsysteme revolutionieren die Produktion
Hochauflösende Kameras scannen bis zu 500 Einheiten pro Minute. Sie analysieren Farbe, Form und Textur mit einer Genauigkeit von 99,7%. Ein Beispiel: Verpackungsfehler werden in Millisekunden erkannt – lange bevor Ware das Lager verlässt.
Die Bedeutung solcher Systeme zeigt sich in reduzierten Ausschussquoten. Betriebe verzeichnen bis zu 40% weniger Nacharbeit. Gleichzeitig entstehen detaillierte Dokumentationen automatisch – ein entscheidender Beitrag zur Compliance.
Datenströme als Grundlage präventiver Maßnahmen
Echtzeitanalysen verhindern Maschinenausfälle, bevor sie entstehen. Sensoren messen Vibrationen, Temperaturspitzen oder Energieverbrauch. Lernende Systeme nutzen diese Daten, um Wartungsintervalle dynamisch anzupassen.
Die Rolle der Datensynchronisation wird hier besonders deutlich: Cloudbasierte Plattformen verbinden Produktionsdaten mit Lieferketteninformationen. So entsteht ein Frühwarnsystem für gesamte Wertschöpfungsnetzwerke.
Wie Sie dieses Wissen praktisch umsetzen? Interaktive Lernmaterialien vermitteln komplexe Zusammenhänge anschaulich. Die Kombination aus Theorie und Praxis schafft nachhaltige Expertise – genau dort, wo sie benötigt wird.
Integration von KI in Produktions- und Lieferkettenprozesse
Was passiert, wenn Maschinen nicht nur produzieren, sondern Prozesse eigenständig optimieren? Moderne Produktionsnetzwerke nutzen lernfähige Algorithmen, um Materialflüsse und Ressourcen präzise zu synchronisieren. Dieses Potenzial entfaltet sich dort, wo Datenströme menschliche Entscheidungen ergänzen – nicht ersetzen.
Produktionssteuerung im Echtzeitmodus
Sensoren erfassen Maschinenleistung und Energieverbrauch millisekundengenau. Lernende Systeme nutzen diese Daten, um Engpässe vorherzusagen. Ein Praxisbeispiel: Ein Getränkehersteller reduziert Stillstandszeiten um 39% durch prädiktive Wartung.
Die Analyse historischer und aktueller Daten ermöglicht dynamische Anpassungen. Produktionspläne aktualisieren sich automatisch bei Lieferverzögerungen. So entstehen stabile Abläufe – selbst bei schwankender Rohstoffqualität.
Logistik wird transparent und agil
Cloudbasierte Plattformen verbinden Lagerbestände mit Transportkapazitäten. Algorithmen berechnen optimale Routen unter Berücksichtigung von:
- Wetterprognosen
- Energiekosten
- Kundenspezifischen Anforderungen
Ein Molkereibetrieb steigerte seine Lieferpünktlichkeit auf 98,7% durch solche Systeme. Mitarbeiter konzentrieren sich nun auf strategische Aufgaben – Algorithmen übernehmen repetitive Analysen.
Das Potenzial dieser Technologien zeigt sich besonders in Krisensituationen. Automatisierte Umdispositionen verhindern Produktionsausfälle. Gleichzeitig entstehen neue Schulungskonzepte: Mitarbeiter werden zu Datenexperten, die Systeme kontinuierlich verbessern.
Echtzeit-Datenanalyse und Prozessoptimierung in der Qualitätskontrolle
Wie erreichen Unternehmen heute millisekundenschnelle Präzision in der Qualitätssicherung? Die Antwort liegt in vernetzten Sensorsystemen, die Prozesse lückenlos überwachen. Diese Technologien erfassen selbst minimale Abweichungen – und lösen automatisch Korrekturmaßnahmen aus.
Sensorik schafft Transparenz
Moderne Infrarotsensoren messen Temperaturprofile mit 0,1°C Genauigkeit. Spektralanalysen erkennen Fremdpartikel in Rohstoffen, während Kamerasysteme Verpackungsfehler in 360°-Ansicht erfassen. Das Ergebnis: Eine kontinuierliche Qualitätskette ohne Blindstellen.
Ein Praxisbeispiel verdeutlicht die Möglichkeiten: Ein Brauereibetrieb reduziert Energieverbrauch um 18%, indem er Sensordaten mit Rezepturen synchronisiert. Algorithmen passieren Produktionsparameter dynamisch an – basierend auf Echtzeitanalysen.
Datenströme in Aktion
Die Lebensmittelbranche nutzt integrierte Sensorsysteme für:
- Früherkennung von Mikroorganismen
- Automatische Kalibrierung von Abfüllanlagen
- Echtzeit-Reporting an Aufsichtsbehörden
Große Datenmengen werden hier zum Schlüssel: Maschinelles Lernen identifiziert Muster, die menschliche Analysten übersehen. Ein Molkereikonzern verbesserte seine Ausschussquote um 29%, indem er historische Daten mit aktuellen Messwerten verknüpfte.
Diese Technologien schaffen nicht nur bessere Ergebnisse, sondern auch neue Möglichkeiten zur Kostenoptimierung. Die Zukunft gehört Systemen, die Probleme erkennen, bevor sie entstehen – und Lösungen direkt in die Prozesse integrieren.
Nachhaltigkeit und Abfallreduzierung durch KI
Wie lassen sich Umweltschutz und Wirtschaftlichkeit in Einklang bringen? Moderne Technologien schaffen hier neue Synergien. Durch präzise Überwachung von Produktionszyklen reduzieren Betriebe ihren Ressourcenverbrauch signifikant – oft schon in der ersten Einführungsphase.
Ressourceneffizienz neu definiert
Intelligente Systeme analysieren Materialströme in Echtzeit. Sie optimieren:
- Energiebedarf durch adaptive Steuerung
- Wassernutzung mittels prädiktiver Algorithmen
- Verpackungsmaterial durch präzise Bedarfsberechnung
Ein Praxisbeispiel zeigt die Auswirkungen: Ein Gemüseverarbeiter senkte seinen Abfall um 37% innerhalb von 6 Monaten. Diese Erfahrung unterstreicht das Potenzial digitaler Lösungen.
Parameter | Traditionelle Methoden | Moderne Systeme | Verbesserung |
---|---|---|---|
Abfallmenge | 12% der Produktion | 4,8% | -60% |
Energieverbrauch | 235 kWh/t | 178 kWh/t | -24% |
Wassernutzung | 8,3 m³/t | 5,1 m³/t | -39% |
CO2-Emissionen | 1,2 kg/t | 0,7 kg/t | -42% |
Langfristige Sicherheit durch Innovation
Die kontinuierliche Überwachung schafft stabile Qualitätsstandards. Sensoren erkennen Temperaturschwankungen, während Algorithmen Haltbarkeitsprognosen verbessern. Diese Informationen ermöglichen eine präventive Warenrotation.
Betriebe verzeichnen nach der Einführung solcher Systeme:
- 31% weniger Retouren
- 19% höhere Liefertreue
- 43% schnellere Reaktion auf Störfälle
Diese Auswirkungen zeigen: Nachhaltigkeit ist kein Ziel, sondern ein dynamischer Prozess. Mit der richtigen Erfahrung werden ökologische Verantwortung und wirtschaftlicher Erfolg zu natürlichen Partnern.
Fazit
Die Zukunft der Lebensmittelsicherheit beginnt heute mit intelligenten Lösungen. Wie dieser Leitfaden zeigt, sind Schlüsseltechnologien wie Echtzeit-Datenanalyse und prädiktive Sensoren keine Option mehr – sie werden zum Standard. Betriebe, die diese Systeme nutzen, steigern nicht nur ihre Qualität, sondern schaffen langfristige Wettbewerbsvorteile.
Die Kombination aus automatisierten Checks und menschlicher Expertise minimiert Risiken effektiv. Gleichzeitig entstehen neue Möglichkeiten: Cloudbasierte Plattformen synchronisieren Lieferketten, während lernende Algorithmen Ressourcenverbrauch optimieren. Diese Entwicklungen prägen die Branche nachhaltig.
Doch wo liegen die Schlüssel zum Erfolg? Kontinuierliche Schulungen und klare Prozessstandards sind entscheidend. Technische Risiken wie Datenlücken erfordern robuste Sicherheitskonzepte. Hier setzen wir an: Mit praxiserprobten Lösungen für präzise Datenanalyse und skalierbare Integration.
Nutzen Sie dieses Wissen als Sprungbrett. Wir begleiten Sie bei der Umsetzung – für eine Produktion, die Sicherheit, Effizienz und Innovation verbindet. Der erste Schritt beginnt jetzt.