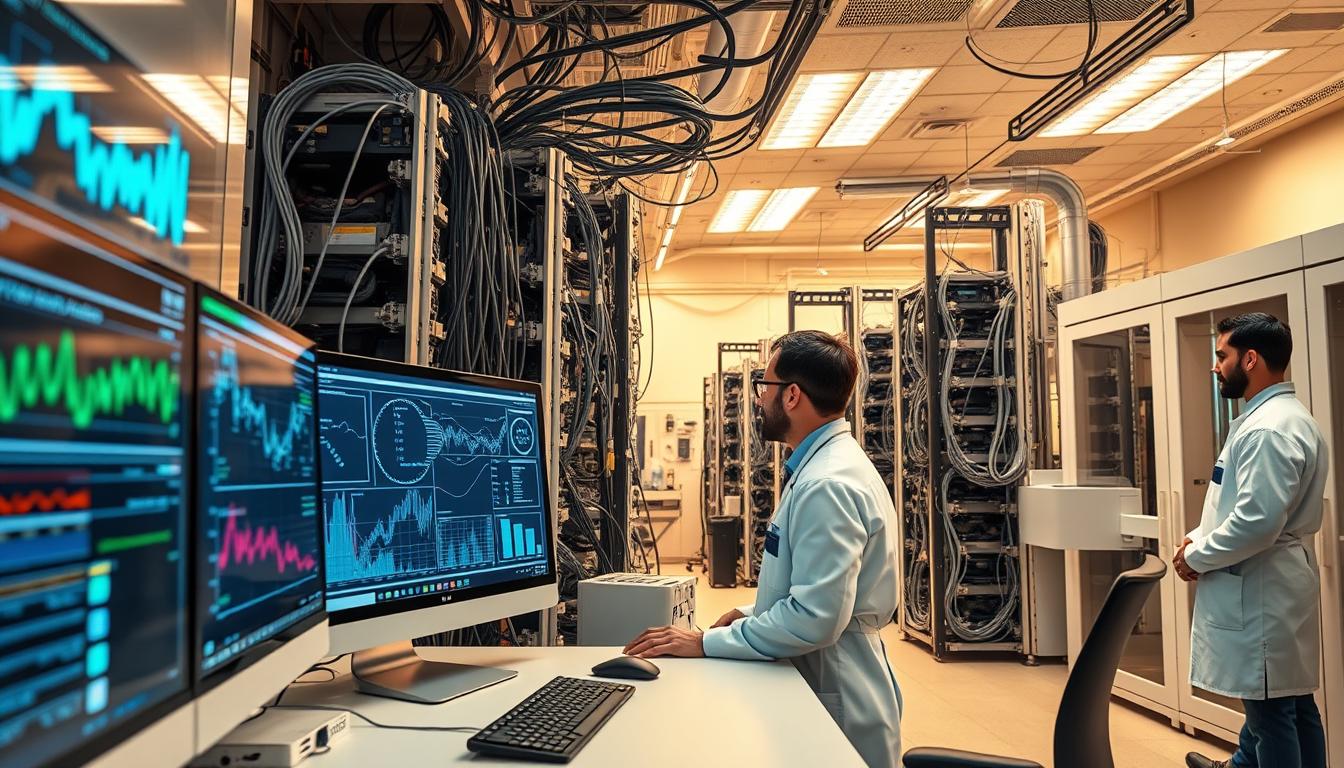
Fehlerursachen vorausschauend erkennen
Können Firmen Fehler wirklich vorhersagen, bevor sie große Probleme verursachen? Die Welt der Reparaturdiagnostik hat eine spannende Antwort: Künstliche Intelligenz verändert, wie wir Störungen analysieren und verhindern.
Störungen in technischen Systemen sind mehr als nur ein Ärgernis. Sie kosten Geld, reduzieren die Produktivität und können sogar gefährlich sein. Moderne Technologien helfen, diese Probleme früh zu erkennen und zu lösen.
Unsere Experten zeigen, wie Firmen durch kluge Wartungsstrategien weniger Stillstand und Kosten sparen können. Die KI in der Reparaturdiagnostik bringt neue Wege für das Fehlermanagement.
Wichtigste Erkenntnisse
- Frühzeitige Erkennung von Störungsursachen durch KI
- Reduzierung von unerwarteten Systemausfällen
- Signifikante Kosteneinsparungen durch präventive Wartung
- Erhöhung der Gesamteffizienz technischer Systeme
- Transformation reaktiver in proaktive Wartungsstrategien
Grundlagen der vorausschauenden Fehleranalyse
Die vorausschauende Analyse hilft Unternehmen, Probleme früh zu erkennen und zu verhindern. Sie ist wichtig für eine moderne Fehlerprävention. Sie minimiert Risiken und spart Kosten.
Definition und Bedeutung für Unternehmen
Eine vorausschauende Analyse nutzt Methoden, um Fehlerquellen früh zu finden. Für Firmen heißt das:
- Frühzeitige Erkennung von Risikofaktoren
- Proaktive Intervention in kritischen Systemen
- Minimierung unerwarteter Produktionsausfälle
Wirtschaftliche Auswirkungen von Störungen
Ungeloste Störungen können teuer werden. Eine gute Fehlerprävention hilft, diese Kosten zu senken.
Störungsart | Durchschnittliche Kosten | Präventionsaufwand |
---|---|---|
Maschinenstillstand | 5.000 – 50.000 € | 500 – 2.000 € |
Produktionsausfall | 10.000 – 100.000 € | 1.000 – 5.000 € |
Präventive vs. reaktive Fehlererkennung
Präventive und reaktive Fehlererkennung unterscheiden sich in ihrer strategischen Ausrichtung. Präventive Methoden antizipieren Probleme. Reaktive Methoden reagieren erst nach dem Problem.
- Präventiv: Vorausschauende Analyse, kontinuierliche Überwachung
- Reaktiv: Reparatur nach Schadenseintritt, höhere Gesamtkosten
Investitionen in vorausschauende Analyse bringen langfristig Vorteile. Sie senken Ausfallzeiten und optimieren Prozesse.
Systematische Erfassung von Störungsmustern
Die Datenerfassung ist der erste Schritt zu einer erfolgreichen Störungsanalyse. Unternehmen müssen Methoden entwickeln, um Störungsmuster genau zu erkennen und zu verstehen.
Wir empfehlen folgende Strategien für die Erfassung von Störungsmustern:
- Digitale Dokumentationssysteme einführen
- Standardisierte Meldeprotokolle entwickeln
- Automatisierte Datenerfassungstechnologien nutzen
- Qualitative und quantitative Analysemethoden kombinieren
Durch gezielte Datensammlung können Unternehmen kritische Schwachstellen früh erkennen. So können sie präventive Maßnahmen ergreifen.
Analysemethode | Fokus | Zeitaufwand |
---|---|---|
Statistische Datenanalyse | Quantitative Fehleridentifikation | Mittel |
Prozessbasierte Mapping | Strukturelle Schwachstellen | Hoch |
Maschinelles Lernen | Prädiktive Fehlererkennung | Niedrig |
Die Nutzung moderner Analysemethoden bietet klare Einblicke in Störungsmuster. Sie hilft Unternehmen, ihre Prozesse ständig zu verbessern.
KI in der Reparaturdiagnostik
Die moderne Industrie verändert sich schnell durch neue Technologien. Künstliche Intelligenz hilft dabei, Wartung und Diagnose zu verbessern. Durch Maschinelles Lernen können Fehler früh erkannt werden. Das spart Unternehmen viel Geld und Zeit.
Maschinelles Lernen zur Fehlererkennung
Maschinelles Lernen verändert die Fehlerdiagnose. KI-gestützte Diagnose ist anders als alte Methoden:
- Automatische Erkennung komplexer Fehlermuster
- Echtzeitanalyse von Maschinendaten
- Präzise Vorhersage potenzieller Störungen
Predictive Maintenance Systeme
Predictive Maintenance ist wichtig für moderne Wartung. Diese Systeme nutzen KI, um:
- Verschleißzustände frühzeitig zu erkennen
- Wartungsintervalle zu optimieren
- Ungeplante Stillstandszeiten zu minimieren
Datenbasierte Analysemethoden
Fortschrittliche Analysemethoden sind der Schlüssel zum Erfolg. Hochentwickelte KI-Systeme analysieren große Datenmengen. So können Unternehmen Risiken verringern und ihre Effizienz steigern.
Implementierung eines Störgrundkatalogs
Ein effektiver Störgrundkatalog ist wichtig für die Fehleranalyse in Unternehmen. Er hilft, Störungen schnell und systematisch zu katalogisieren. Das steigert die Effizienz bei der Fehlererkennung.
Bei der Implementierung eines Störgrundkatalogs gibt es wichtige Punkte:
- Klare Standardisierung der Erfassungskriterien
- Einfache und intuitive Kategorisierung
- Flexibilität für verschiedene Anwendungsbereiche
- Digitale Dokumentationsmöglichkeiten
Die Kategorisierung ist das Herz eines guten Störgrundkatalogs. Sie hilft Mitarbeitern, Fehlerquellen genau zu finden und zu klassifizieren.
Kategorie | Beschreibung | Priorität |
---|---|---|
Technische Störungen | Mechanische und elektronische Fehlfunktionen | Hoch |
Prozessbedingte Fehler | Ablaufstörungen in Arbeitsabläufen | Mittel |
Menschliche Fehler | Fehler durch Bedienungsfehler | Niedrig |
Standardisierung sorgt für eine einheitliche Dokumentation. Wichtig ist eine klare Struktur, die sowohl detaillierte Analysen als auch schnelle Einordnungen ermöglicht.
Unser Ziel ist es, Ihnen ein nützliches Werkzeug zu geben. Es soll Ihre Störungsanalyse verbessern und die Prozessqualität steigern.
Methoden der Früherkennung von Fehlerquellen
Die Erkennung von Fehlerquellen ist sehr wichtig für die Qualität in technischen Systemen. Viele Firmen nutzen moderne Methoden, um Risiken früh zu erkennen. So können sie Störungen verhindern.
FMEA: Systematische Fehlererkennung
Die FMEA ist eine starke Methode zur Vorhersage von Fehlern. Sie ermöglicht eine strukturierte Bewertung von möglichen Fehlerquellen schon in der Entwicklungsphase.
- Identifikation potenzieller Fehlerarten
- Bewertung der Auswirkungen von Störungen
- Priorisierung von Risiken
- Entwicklung präventiver Maßnahmen
Ishikawa-Diagramm: Ursachenanalyse
Das Ishikawa-Diagramm zeigt komplexe Zusammenhänge bei der Fehleranalyse. Es hilft, systematisch Fehlerursachen zu strukturieren.
Hauptkategorie | Mögliche Ursachen |
---|---|
Mensch | Schulungsmängel, Unaufmerksamkeit |
Maschine | Verschleiß, technische Defekte |
Material | Qualitätsschwankungen, Verunreinigungen |
Root Cause Analysis: Tiefgehende Fehleranalyse
Die Root Cause Analysis sucht nach den tiefen Ursachen von Fehlern. Sie geht nicht nur die Symptome an, sondern untersucht die Wurzelursachen. So entwickeln sie nachhaltige Lösungen.
- Problembeschreibung
- Datensammlung
- Ursachenidentifikation
- Lösungsentwicklung
- Implementierung und Überprüfung
Diese Methoden helfen Firmen, Fehlerquellen früh zu erkennen. So können sie proaktiv Maßnahmen für die Qualitätssicherung entwickeln.
Technische Systeme zur Störungsprävention
Die moderne Industrie nutzt fortschrittliche Sensortechnologie, um Probleme früh zu erkennen. Überwachungssysteme sind wichtig, um den Produktionsablauf reibungslos zu halten.
Moderne Frühwarnsysteme geben Unternehmen Einblick in ihre technischen Anlagen. Sie ermöglichen es, Risiken frühzeitig zu erkennen. Dies geschieht durch intelligente Datenerfassung und -auswertung.
- Kontinuierliche Zustandsüberwachung
- Echtzeit-Fehleranalyse
- Predictive Maintenance
Die Einführung von Sensortechnologie in bestehende Systeme braucht strategische Planung. Unternehmen müssen Messpunkte genau auswählen, um die besten Ergebnisse zu erzielen.
Technologie | Funktionalität | Nutzen |
---|---|---|
Vibrationsanalyse | Mechanische Zustandsüberwachung | Früherkennung von Maschinenverschleiß |
Thermografiesensoren | Temperaturüberwachung | Verhinderung von Überhitzung |
Akustische Emissionssensoren | Geräuschanalyse | Identifikation struktureller Veränderungen |
Die Einführung moderner Frühwarnsysteme hilft Unternehmen, Fehler frühzeitig zu erkennen. Durch Investitionen in Sensortechnologie können Ausfälle reduziert und Wartungskosten gesenkt werden.
Dokumentation und Analyse von Störfällen
Die systematische Erfassung und Auswertung von Störungsdaten ist sehr wichtig. Es hilft, Fehler zu erkennen und Prozesse zu optimieren. Unsere Experten erklären, wie man Störfälle gut dokumentiert und analysiert.
Strukturierte Erfassung von Störungsdaten
Eine genaue Störungsdokumentation ist sehr wichtig. Es hilft, technische Probleme zu verstehen. Hier sind einige Schritte für die Datenerfassung:
- Detaillierte Beschreibung des Störungshergangs
- Exakte Zeitstempel der Ereignisse
- Identifikation betroffener Komponenten
- Dokumentation möglicher Auslöser
Auswertungsmethoden und Tools
Moderne Analysesoftware ermöglicht tiefe Datenauswertungen. Wir empfehlen professionelle Software, die viele Funktionen bietet:
- Automatische Mustererkennung
- Statistische Trendanalysen
- Grafische Visualisierung von Störungsmustern
- Präzise Fehlerwahrscheinlichkeitsberechnungen
Die richtige Kombination aus Dokumentation und Analyse-Software ist sehr wichtig. Sie hilft, Fehler zu vermeiden und Prozesse zu verbessern.
Mitarbeiterqualifikation zur Fehlererkennung
Die Entwicklung von Kompetenzen ist sehr wichtig für die Störungsanalyse. Gut ausgebildete Mitarbeiter erkennen Fehler früh. Moderne Schulungsprogramme verbessern ihre Fähigkeiten.
Fehler erkennen zu können, braucht mehr als nur Wissen. Es geht um eine ganzheitliche Herangehensweise. Dazu gehören:
- Analytisches Denken zur Identifikation von Störungsmustern
- Technisches Verständnis für komplexe Systemzusammenhänge
- Proaktive Problemerkennungsfähigkeiten
Die Schulungen müssen praktisch sein. Interaktive Trainingsmethoden wie Simulationen und Fallstudien sind hilfreich. Digitale Lernplattformen unterstützen die ständige Weiterbildung.
Unternehmen, die in Mitarbeiterqualifikation investieren, schaffen eine Kultur der vorausschauenden Störungsprävention. Durch Weiterbildung werden Mitarbeiter zu Problemlösern.
Integration in bestehende QM-Systeme
Um Störungsprävention in Qualitätsmanagement erfolgreich zu integrieren, braucht es eine kluge Planung. Unternehmen müssen ihre Abläufe anpassen, um am besten zu funktionieren.
- Qualitätsmanagement-Dokumentationen gründlich prüfen
- Neue Präventionsmethoden in Anweisungen einfügen
- Optimierung der Schnittstellen zwischen Abteilungen
- Mitarbeiter schulen und sensibilisieren
Prozessintegration präzise gestalten
Bei der Prozessintegration ist eine ganzheitliche Betrachtungsweise entscheidend. Man muss Stellenbeschreibungen anpassen und neue Verantwortlichkeiten einrichten. Digitale Hilfsmittel wie künstliche Intelligenz können dabei unterstützen.
Effektives Schnittstellenmanagement
Ein gutes Schnittstellenmanagement verringert Kommunikationsprobleme zwischen Abteilungen. Es ist wichtig, klare Verantwortlichkeiten zu definieren und standardisierte Informationsflüsse zu etablieren.
Die Verbindung von Qualitätsmanagement und Störungsprävention schafft ein starkes System. Es erkennt Fehler früh und behandelt sie proaktiv.
Wirtschaftlichkeitsbetrachtung präventiver Maßnahmen
Störungen in Unternehmensprozessen können viel Geld kosten. Eine genaue Analyse hilft, kluge Entscheidungen zu treffen. So können Unternehmen große Verluste vermeiden.
Um den Nutzen von Präventionskosten zu berechnen, muss man genau hinschauen. Man muss die Kosten für Vorbeugung gegen die möglichen Kosten von Unterbrechungen abwägen.
- Identifizierung von Hauptrisikobereichen
- Quantifizierung der Präventionskosten
- Bewertung der erwarteten Einsparungen
- Berechnung des langfristigen finanziellen Nutzens
Moderne Unternehmen nutzen künstliche Intelligenz für bessere Präventionsstrategien. Sie analysieren Daten, um ihre Wartung zu verbessern und Kosten zu senken.
Präventive Maßnahmen bringen langfristig Vorteile. Unternehmen, die Risiken verringern, bleiben produktiv und wettbewerbsfähig. Eine kluge Strategie steigert die Effizienz.
Experten raten, die Präventionsstrategien regelmäßig zu überprüfen. So stellen man sicher, dass die Investitionen gut sind. Die Analyse muss sich ständig anpassen.
Best Practices aus der Industrie
Effiziente Präventionsstrategien brauchen einen tiefen Erfahrungsaustausch. Industriebeispiele zeigen, wie moderne Technologien Fehler früh erkennen.
Erfolgsgeschichten aus verschiedenen Branchen betonen die Wichtigkeit von vorausschauenden Strategien. Unternehmen, die künstliche Intelligenz in die Qualitätssicherung bringen, sehen große Fortschritte.
Praktische Implementierungsbeispiele
- Automobilindustrie: Einsatz von KI-gestützten Predictive-Maintenance-Systemen
- Maschinenbau: Entwicklung intelligenter Fehlererkennungsalgorithmen
- Elektronikproduktion: Digitale Echtzeitüberwachung von Fertigungsprozessen
Präventive Strategien senken Ausfallzeiten und Reparaturkosten stark.
Lessons Learned
Branche | Herausforderung | Lösung |
---|---|---|
Automotive | Komplexe Maschinenüberwachung | KI-basierte Zustandsanalyse |
Maschinenbau | Unerwartete Produktionsstörungen | Vorausschauende Wartungskonzepte |
Elektronik | Qualitätsschwankungen | Echtzeitmonitoring |
Der Erfahrungsaustausch zwischen Firmen ist wichtig für ständige Verbesserungen in der Fehlerprävention.
Rechtliche Aspekte der Störungsprävention
Störungsprävention ist mehr als nur Technik. Es geht auch um Recht. Unternehmen müssen mit Haftungsrisiken umgehen.
Es gibt klare Gesetze für Firmen. Sie müssen Strategien entwickeln, um Risiken zu vermindern. So bleiben sie rechtlich sicher.
- Identifizierung potenzieller Rechtrisiken
- Entwicklung präventiver Compliance-Maßnahmen
- Dokumentation von Sicherheitsstandards
Umfangreiche Präventionsstrategien schützen vor rechtlichen Problemen. Sie stärken auch das Vertrauen von Kunden und Partnern.
Rechtliche Dimension | Präventive Maßnahmen |
---|---|
Produkthaftung | Systematische Qualitätskontrollen |
Arbeitsschutz | Regelmäßige Sicherheitsschulungen |
Technische Normen | Kontinuierliche Normkonformitätsprüfungen |
Wichtig ist eine ganzheitliche Betrachtung der Rechtssicherheit, die technische, organisatorische und juristische Aspekte miteinander verbindet.
Kontinuierliche Verbesserung der Präventionsmaßnahmen
Der Kontinuierliche Verbesserungsprozess (KVP) ist sehr wichtig für Unternehmen. Er hilft, Maßnahmen zur Vorbeugung von Problemen zu verbessern. Durch spezielle Kennzahlen können Firmen ihre Präventionsmethoden ständig verbessern.
Um erfolgreich zu sein, sollten Unternehmen folgende Schritte befolgen:
- Regelmäßige Datenerfassung und -analyse
- Identifikation von Verbesserungspotentialen
- Entwicklung gezielter Präventionsstrategien
Ein strukturiertes Monitoring-System hilft, Fehler früh zu erkennen. Wichtige Kennzahlen zeigen Schwachstellen auf. So können Maßnahmen schnell entwickelt werden.
Wichtige Teile des KVP sind:
- Systematische Dokumentation von Störfällen
- Kontinuierliche Ursachenanalyse
- Entwicklung präventiver Gegenmaßnahmen
Datenanalyse und Prozessoptimierung sind wichtig für Risikomanagement. So können Firmen ihre Strategien an neue Herausforderungen anpassen.
Fazit
Die präventive Störungsanalyse ist heute sehr wichtig. Sie hilft Unternehmen, sich besser zu entwickeln. Wer frühzeitig in neue Analysemethoden investiert, hat einen großen Vorteil.
Das Potenzial für Neuerungen in der Störungsprävention ist groß. Durch Künstliche Intelligenz und maschinelles Lernen können wir besser vorhersagen und sparen Ressourcen. Unternehmen, die diese Technologien nutzen, können ihre Ausfallzeiten stark reduzieren.
Wichtig ist, dass Unternehmen ihre Technik immer weiterentwickeln. Die Nutzung von Datenanalyse wie FMEA wird zukünftig unverzichtbar sein. Es ist eine Grundlage für starke und widerstandsfähige Produktionssysteme.
Beginnen Sie jetzt, Ihre Störungsanalyse zu verbessern. Die Reise zur proaktiven Instandhaltung startet mit dem ersten Schritt. Machen Sie diesen Schritt heute.
FAQ
Was ist präventive Störungsanalyse?
Wie unterscheidet sich präventive von reaktiver Fehlererkennung?
Welche Rolle spielt Künstliche Intelligenz in der Störungsanalyse?
Welche Methoden gibt es zur Früherkennung von Fehlerquellen?
Wie kann ich Mitarbeiter in die Störungsprävention einbeziehen?
Was bringen technische Systeme zur Störungsprävention?
Wie wirtschaftlich sind präventive Maßnahmen?
Welche rechtlichen Aspekte muss ich bei der Störungsprävention beachten?
Tag:Datengetriebene Fehlerprävention, Diagnose-Technologien für industrielle Anlagen, Fehlerursachenanalyse, Künstliche Intelligenz in der Reparaturdiagnostik, Maschinelles Lernen in der Instandhaltung, Optimierung von Reparaturprozessen, Prädiktive Analytik bei Reparaturen, Proaktive Instandhaltungsmethoden, Vorausschauende Wartung, Wartungsstrategien in der Industrie 4.0