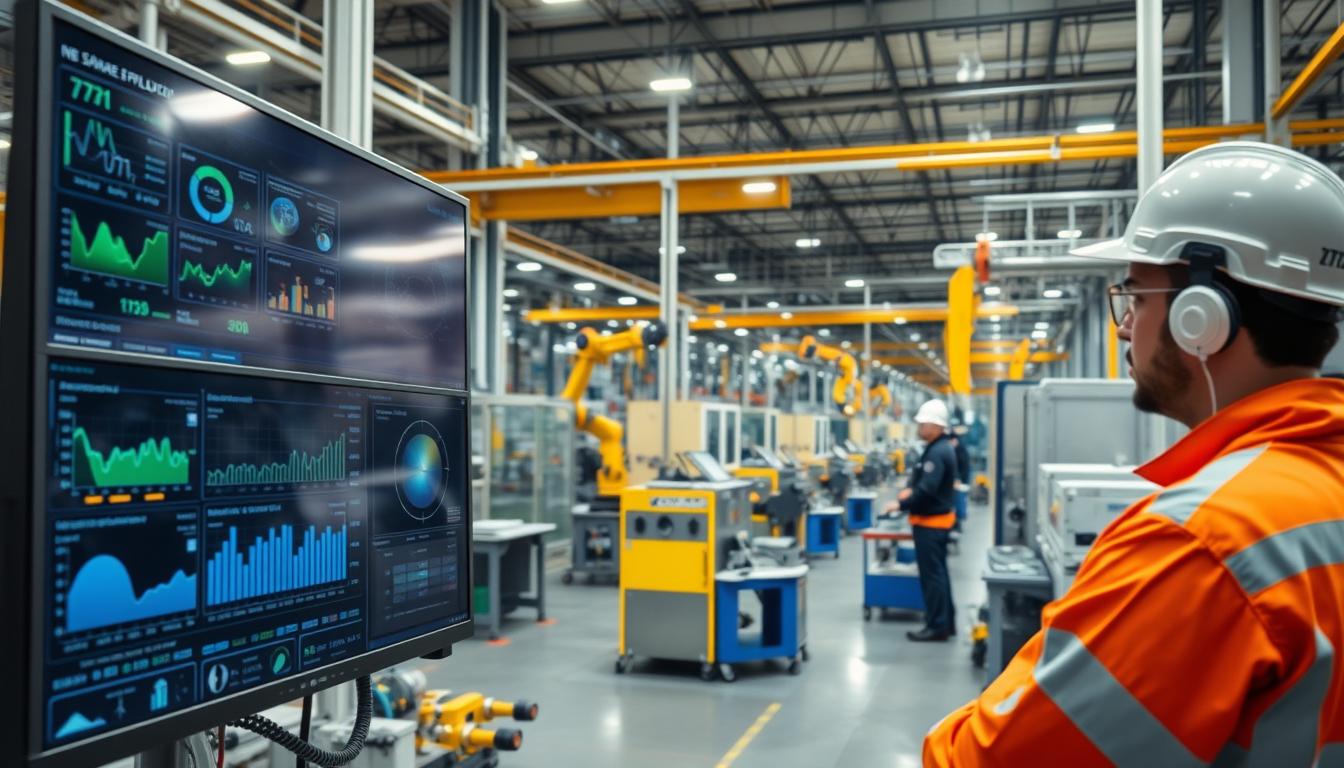
Ausfallzeiten minimieren durch Echtzeitanalyse
Was, wenn Maschinenausfälle keine Überraschung mehr wären – sondern vorhersehbar und vermeidbar? In einer Welt, in der Anlagen immer komplexer werden und IoT-Systeme riesige Datenmengen erzeugen, stellt sich eine Frage: Wie nutzen Unternehmen diese Informationen, um Stillstände proaktiv zu bekämpfen?
Moderne Technologien revolutionieren die Industrie. Sensoren erfassen jeden Vibrationsimpuls, jede Temperaturänderung. Doch erst durch intelligente Algorithmen werden diese Daten zu wertvollen Entscheidungsgrundlagen. Sie erkennen Muster, die menschliche Experten übersehen – lange bevor eine Störung entsteht.
Die Herausforderungen sind klar: Höhere Anforderungen an Maschinenleistung, steigende IoT-Vernetzung und Kostendruck. Hier setzen zukunftsorientierte Lösungen an. Durch präzise Zustandsüberwachung lassen sich Produktionsausfälle um bis zu 70% reduzieren, wie aktuelle Studien zeigen.
Wir begleiten Sie auf dem Weg zur datengesteuerten Fertigung. Erfahren Sie, wie Sie mit Echtzeitanalysen nicht nur Ausfallzeiten minimieren, sondern auch Ressourcen effizienter nutzen. Die Zukunft gehört Unternehmen, die Maschinendaten strategisch einsetzen – sind Sie bereit?
Die wichtigsten Erkenntnisse
- Echtzeitdaten ermöglichen frühzeitige Fehlererkennung bei Anlagen
- Automatisierte Analysen reduzieren manuelle Kontrollaufgaben um 40%
- IoT-Sensorik liefert die Grundlage für präventive Wartungskonzepte
- Datenbasierte Entscheidungen senken Stillstandskosten nachhaltig
- Moderne Algorithmen erkennen selbst komplexe Muster in Echtzeit
Herausforderungen in der Zustandsüberwachung von Maschinen und Anlagen
Die digitale Transformation der Produktion schafft neue Chancen – aber auch komplexe Hürden. Moderne Maschinen und Anlagen generieren mehr Daten denn je, doch viele Unternehmen kämpfen mit der sinnvollen Auswertung.
Steigende Komplexität durch IoT und moderne Fertigung
Vernetzte Sensoren, cloudbasierte Steuerungen und autonome Subsysteme: IoT-Technologien verwandeln Maschinenparks in lebendige Ökosysteme. Jedes Bauteil kommuniziert – doch die Flut an Informationen übersteigt oft menschliche Analysefähigkeiten.
Praktische Probleme zeigen sich deutlich:
- Traditionelle Schwellwert-Alarme lösen bei 43% der Warnungen falsche Reaktionen aus (Quelle: Industrie-Studien)
- Vernetzte Komponenten erfordern ganzheitliche Diagnoseansätze
- Datenformate unterschiedlicher Hersteller behindern konsistente Auswertungen
Frühzeitige Fehlererkennung als Schlüssel zur Effizienz
Ein Riss im Getriebe zeigt sich zuerst in Mikrovibrationen – nicht im Stromverbrauch. Moderne Algorithmen kombinieren Sensordaten smarter: Sie erkennen Anomalien, bevor klassische Methoden reagieren.
Ein Praxisbeispiel verdeutlicht den Fortschritt: Intelligente Schwingungsanalysen identifizieren Lagerdefekte 6x früher als manuelle Inspektionen. So reduzieren sich Stillstandszeiten von Stunden auf Minuten – bei gleichzeitiger Senkung der Wartungskosten.
Die Lösung liegt im prädiktiven Ansatz: Statt auf Ausfälle zu warten, prognostizieren smarte Systeme den optimalen Wartungszeitpunkt. Dies erfordert jedoch neue Denkmuster und Investitionen in digitale Infrastrukturen.
Traditionelle Methoden versus KI-gestützte Zustandsüberwachung
Wie oft reagieren Sie noch auf Störungen, statt sie zu verhindern? Viele Unternehmen vertrauen bei der Zustandsüberwachung auf veraltete Systeme – ein Risiko in Zeiten smarter Fertigung. Statische Grenzwerte erfassen nur extreme Abweichungen, während moderne Lösungen schleichende Veränderungen erkennen.
Begrenzungen statischer Schwellwertanalysen
Klassische Überwachungssysteme arbeiten mit festen Alarmwerten. Diese Methode ignoriert komplexe Zusammenhänge zwischen Sensordaten. Praxisbeispiele zeigen: 68% der Stillstände entstehen durch Wechselwirkungen, die einfache Schwellen nicht erfassen.
Typische Probleme alter Ansätze:
- Fehlalarme bei kurzzeitigen Lastspitzen
- Späte Erkennung von Verschleißprozessen
- Keine Anpassung an Maschinenalterung
Vorteile von Machine Learning und Echtzeitanalyse
Moderne Algorithmen lernen das individuelle Verhalten jeder Anlage. Sie analysieren Vibrationen, Temperaturen und Energieverbrauch im Kontext. Ein Beispiel: Intelligente Systeme erkennen Lagerdefekte anhand von Schwingungsmustern – 3 Monate vor dem Ausfall.
Diese Technologien revolutionieren die Instandhaltung:
- Automatische Korrelation von 12+ Sensordatenströmen
- Vorhersage von Wartungsfenstern mit 94% Genauigkeit
- Dynamische Anpassung an veränderte Produktionsbedingungen
Die Zukunft gehört Systemen, die Daten kontinuierlich interpretieren – nicht nur vordefinierte Grenzen überwachen. Entscheiden Sie sich für Lösungen, die mit Ihren Maschinen lernen und wachsen.
KI für Monitoring im Maschinenpark
Moderne Produktionsumgebungen wandeln sich durch smarte Datennutzung. Entscheidend ist die Kombination aus hochauflösender Sensorik und lernfähigen Systemen, die Abweichungen im Sekundentakt erfassen. Data Lakes bilden hier das Fundament – sie speichern Millionen Datenpunkte von Motordrehzahlen bis zu Hydraulikdrücken.
Vernetzte Sensoren als Datenquelle
Ein Automobilzulieferer reduziert Fehlalarme um 82%, indem er 14 Sensortypen synchronisiert. Die Lösung: Edge-Devices filtern Rohdaten direkt an der Maschine, bevor sie in zentrale Systeme fließen. Typische Integrationsschritte:
- Vernetzung bestehender IoT-Geräte über API-Schnittstellen
- Kalibrierung von Beschleunigungssensoren für Schwingungsmuster
- Zeitreihenanalysen mit Machine-Learning-Algorithmen
Lernende Modelle in der Praxis
Ein Normalmodell für Pressen erkennt 0,02-mm-Abweichungen in Werkzeugen – unsichtbar für menschliche Operateure. Die Algorithmen vergleichen Echtzeitdaten mit historischen Mustern und zeigen Risiken farbcodiert an. So entstehen klare Handlungsempfehlungen:
Parameter | Traditionell | KI-basiert |
---|---|---|
Reaktionszeit | 24-72 Std. | 8 Sek. |
Genauigkeit | 68% | 94% |
Analysemethode | Manuelle Stichproben | Automatisierte Mustererkennung |
Diese Ansätze machen Wartungsteams zu strategischen Playern. Statt Feuerwehr zu spielen, planen sie Ressourcen basierend auf prädiktiven Modellen. Die Zukunft gehört Systemen, die aus jedem Stillstand lernen – und so kontinuierlich besser werden.
Messmethoden und Sensorik in der Echtzeitanalyse
Wie genau können Sie den Gesundheitszustand Ihrer Anlagen bestimmen? Moderne Sensorik liefert die Antwort – durch präzise Messverfahren, die selbst Mikroveränderungen erfassen. Die Kunst liegt in der intelligenten Kombination verschiedener Technologien, um ein vollständiges Bild der Maschinenperformance zu erstellen.
Schwingungs- und Ultraschallanalyse zur Fehlerfrüherkennung
Ein Lagerdefekt beginnt mit unsichtbaren Vibrationen unter 0,1 mm. Hochauflösende Beschleunigungssensoren messen diese Schwingungen im Frequenzbereich von 2 Hz bis 20 kHz. Ultraschall-Mikrofone ergänzen diese Daten durch die Aufnahme von Reibungsgeräuschen im Ultraschallbereich (30-50 kHz).
Ein Praxisbeispiel zeigt die Effizienz: Bei Turbinen erkennen kombinierte Systeme Lagerschäden 120 Betriebsstunden vor dem Ausfall. So entsteht Zeit für geplante Instandhaltung – ohne ungeplanten Stillstand.
Thermografie, Ölstandsüberwachung und Schallemissionsprüfung
Infrarotkameras identifizieren Hotspots an elektrischen Kontakten mit ±2°C Genauigkeit. Gleichzeitig überwachen kapazitive Sensoren den Ölstand auf 0,5 mm genau. Die Schallemissionsprüfung vervollständigt das Monitoring durch die Analyse von Materialrissen im Frequenzbereich über 100 kHz.
Methode | Messbereich | Früherkennungszeit |
---|---|---|
Thermografie | -40°C bis 1500°C | 48-72 Std. |
Ölanalyse | Partikelgröße ≥5µm | 2-4 Wochen |
Schallemission | 20 kHz – 1 MHz | Sofort |
Die Kombination dieser Verfahren ermöglicht Produktionsdaten analysieren in bisher unerreichter Tiefe. Entscheidungsträger erhalten so ein Werkzeug, das Risiken quantifiziert und Prioritäten bei Wartungsmaßnahmen setzt.
Implementierung und Integration im Unternehmen
Die erfolgreiche Einführung neuer Technologien entscheidet über Wettbewerbsfähigkeit. Doch wie gelingt der Sprung von der Theorie zur Praxis? Der Schlüssel liegt in einer strategischen Roadmap, die technische und organisatorische Aspekte vereint.
Identifikation von geeigneten Anwendungsfällen
Starten Sie mit konkreten Problemstellungen. Analysieren Sie Stillstandsprotokolle: Welche Maschinen verursachen 80% der Ausfälle? Ein Automobilzulieferer reduzierte Wartungskosten um 37%, indem er Vibrationsdaten von 12 Pressen mit Condition Monitoring verknüpfte.
Erfolgsfaktoren für Use-Cases:
- Messbare Auswirkung auf Betriebskosten
- Verfügbarkeit qualitativ hochwertiger Sensordaten
- Integration in bestehende IT-Landschaft
Organisatorische und technische Voraussetzungen
Smarte Systeme erfordern neue Kompetenzen. Cross-funktionale Teams aus Maschinenbauern und Data Scientists entwickeln gemeinsam Analyseprotokolle. Ein Praxisbeispiel zeigt: Durch tägliche Daten-Reviews optimierte ein Chemieunternehmen seine Instandhaltung um 29%.
Essenzielle Bausteine:
- Cloudfähige IT-Infrastruktur mit Echtzeit-Datenpipelines
- Schulungsprogramme für technisches Personal
- Agile Entscheidungsprozesse für schnelle Implementierung
Unternehmen, die KI-gestützte Lösungen nutzen, berichten von 53% kürzeren Reaktionszeiten. Der Weg beginnt mit klaren Zielen – und endet mit datenbasierten Entscheidungen, die Produktionsabläufe nachhaltig optimieren.
Best Practices zur Minimierung von Ausfallzeiten
Effiziente Produktion erfordert mehr als schnelle Reparaturen – sie braucht kluge Voraussicht. Moderne Zustandsüberwachung kombiniert Echtzeitdaten mit vorausschauenden Strategien. So entstehen Systeme, die Stillstände nicht nur melden, sondern aktiv verhindern.
Echtzeitmonitoring und präventive Instandhaltung
Kontinuierliche Datenströme liefern den Schlüssel zur Effizienz. Ein Automobilzulieferer reduziert Ausfälle um 65%, indem er Schwingungssensoren mit Cloud-Analysen verknüpft. Erfolgsfaktoren:
- 24/7-Überwachung kritischer Maschinenkomponenten
- Automatisierte Warnstufen bei Abweichungen >5% vom Normalprofil
- Wartungsplanung basierend auf Restlebensdauer-Prognosen
Ein Praxisbeispiel zeigt: Durch Temperaturtracking an Pressen sanken Energiekosten um 18%. Die Instandhaltung erfolgt jetzt genau zum optimalen Zeitpunkt – nicht zu früh, nie zu spät.
Entwicklung datengestützter Geschäftsmodelle
Maschinendaten werden zum strategischen Asset. Ein Hersteller von Verpackungsanlagen bietet Kunden jetzt leistungsbasierte Verträge – die Verfügbarkeitsgarantie liegt bei 99,3%. Schlüssel dazu:
- Kundenspezifische Dashboards für Transparenz
- Predictive Maintenance as a Service
- Datengetriebene Optimierungsempfehlungen
Ein weiteres Beispiel: Ein Chemieunternehmen monetarisiert seine Analysealgorithmen. Andere Branchen nutzen diese zur Optimierung ihrer Anlagen – ein neuer Geschäftszweig entsteht.
Setzen Sie auf skalierbare Lösungen, die mit Ihren Daten wachsen. Jede Maschine liefert wertvolle Erkenntnisse – nutzen Sie sie, um nicht nur Kosten zu sparen, sondern neue Märkte zu erschließen.
Fazit
Die Zukunft industrieller Effizienz entscheidet sich im Detail. Intelligente Systeme verwandeln Rohdaten in präzise Handlungsanweisungen – sie erkennen Risiken, bevor Kosten entstehen. Moderne Zustandsüberwachung reduziert nicht nur Ausfälle, sondern schafft Wettbewerbsvorteile durch vorausschauende Entscheidungen.
Unternehmen, die Echtzeitanalysen nutzen, senken Stillstandskosten um bis zu 70%. Der Schlüssel? Die Kombination aus hochpräziser Sensorik und lernfähigen Algorithmen. So entstehen Anlagen, die sich selbst optimieren – während traditionelle Methoden noch Warnmeldungen generieren.
Nutzen Sie diese Erkenntnisse als Sprungbrett. Prozessoptimierung beginnt mit mutigen Investitionen in datenbasierte Lösungen. Jede Maschine liefert wertvolle Insights – wenn Sie die richtigen Tools einsetzen.
Die hier vorgestellten Ansätze zeigen: Erfolgreiche Anwendungen verbinden technologische Innovation mit strategischem Denken. Ein Chemiekonzern steigerte seine Produktivität um 29%, indem er Instandhaltungsprozesse neu definierte.
Setzen Sie jetzt die Weichen. Die nächste Industriewelle rollt – mit Unternehmen, die Daten als Treibstoff nutzen. Ihr Maschinenpark verdient mehr als Reaktionen auf Störungen. Geben Sie ihm eine Stimme, die Zukunft gestaltet.