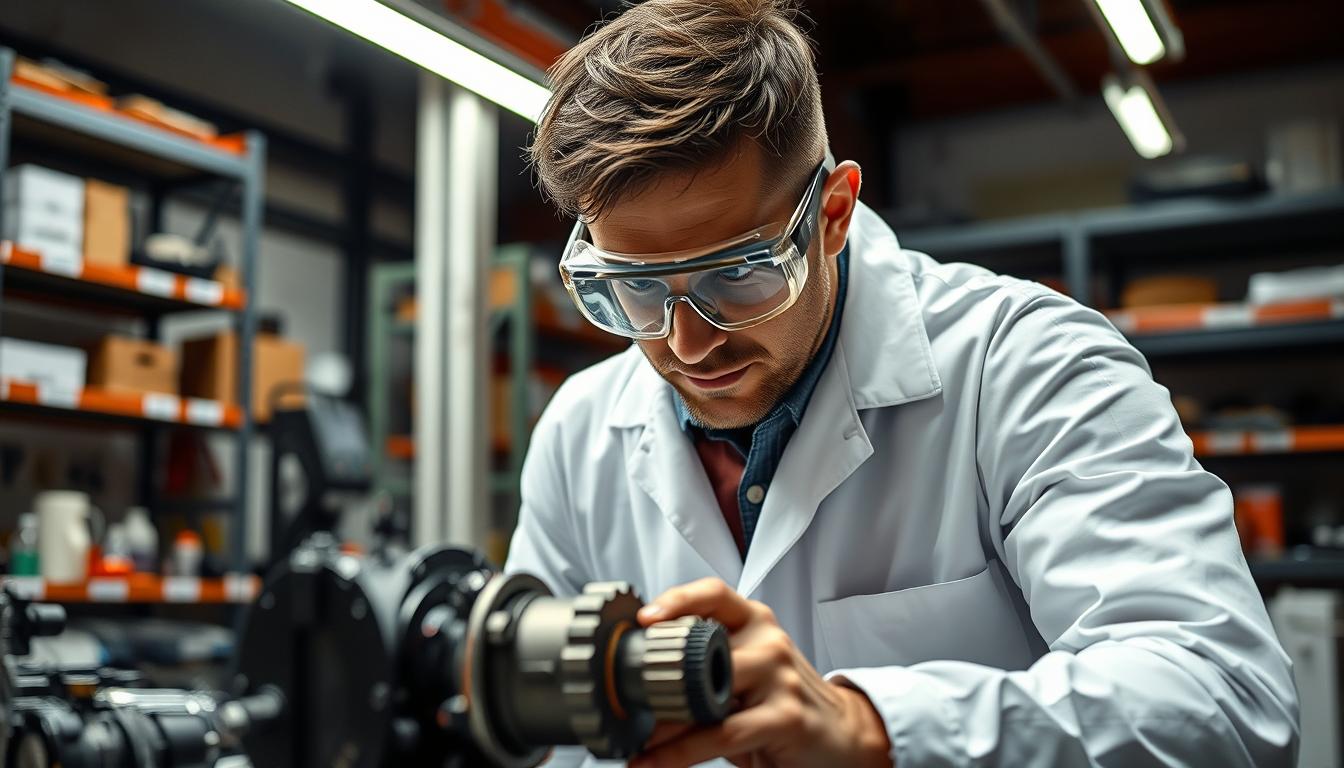
Abweichungen erkennen und Maßnahmen vorschlagen
Haben Sie sich jemals gefragt, warum selbst etablierte Prozesse kritische Fehler übersehen – trotz penibler manueller Kontrollen? Die Antwort liegt nicht in mangelnder Sorgfalt, sondern in der Komplexität moderner Produktionsketten. Hier setzt eine revolutionäre Methode an, die traditionelles Qualitätsmanagement neu definiert.
Intelligente Systeme analysieren heute Millionen Datensätze in Echtzeit. Sie identifizieren Abweichungen, die menschliche Experten nie entdecken würden. Diese Technologie ist kein Ersatz, sondern eine strategische Erweiterung bewährter Methoden. Sie kombiniert menschliche Expertise mit präziser Datenauswertung.
Warum gewinnt dieser Ansatz rasant an Bedeutung? Branchenstudien zeigen: Unternehmen erreichen durch automatisierte Fehlerfrüherkennung bis zu 40% höhere Prozesseffizienz. Gleichzeitig sinken Nachbearbeitungskosten signifikant. Der Schlüssel liegt in transparenter Algorithmen-Architektur, die Entscheidungen nachvollziehbar macht.
Schlüsselerkenntnisse
- Moderne Technologien erweitern das Methodenspektrum im Qualitätsmanagement
- Echtzeitdatenanalyse ermöglicht präventive Fehlererkennung
- Transparente Algorithmen schaffen Vertrauen in automatisierte Lösungen
- Kosteneinsparungen durch reduzierte Nacharbeit und Stillstandszeiten
- Wettbewerbsvorteile durch kontinuierliche Prozessoptimierung
Führende Unternehmen nutzen bereits intelligente Lösungen, um Qualität messbar zu steigern. Diese Entwicklung ist kein Zufall, sondern Antwort auf globale Lieferketten und steigende Kundenerwartungen. Wie Sie diese Innovationen praktisch umsetzen? Wir führen Sie durch die wichtigsten Schritte.
: Einführung in KI im Qualitätswesen
Innovative Ansätze revolutionieren das Qualitätsmanagement in Echtzeit. Sie verbinden maschinelle Präzision mit menschlicher Expertise – eine Symbiose, die bisher undenkbar schien. Datenbasierte Entscheidungen werden zum Treiber für fehlerfreie Produktionsprozesse und kundenorientierte Lösungen.
Relevanz und aktuelle Trends
Cloud-basierte Systeme und generative Algorithmen dominieren die Praxis. Diese Tools analysieren nicht nur Fehlerquellen, sondern prognostizieren Risiken bevor sie entstehen. Eine aktuelle Studie belegt: 78% der Industrieunternehmen nutzen bereits lernfähige Software für Qualitätschecks.
Drei Schlüsselentwicklungen prägen 2024:
- Echtzeit-Diagnostik über vernetzte Sensoren
- Selbstoptimierende Prüfprotokolle
- Vorausschauende Wartungsalgorithmen
Überblick über den Artikelinhalt
Wir zeigen Ihnen, wie Sie diese Technologien Schritt für Schritt implementieren. Von Grundkonzepten bis zu Pilotprojekten – erfahren Sie, welche Methoden sich in der Praxis bewährt haben. Die folgenden Kapitel beleuchten:
• Technische Voraussetzungen für digitale Transformation
• Bewährte Analyseverfahren im Detail
• Erfolgsbeispiele aus der Automobil- und Pharmabranche
Nutzen Sie dieses Wissen, um Ihre Qualitätsstandards neu zu definieren. Die Zukunft der Fehlerprävention beginnt heute.
: Grundlagen der künstlichen Intelligenz im Qualitätswesen
Wie können traditionelle Methoden mit heutigen Produktionsgeschwindigkeiten mithalten? Die Antwort liegt in intelligenten Systemen, die menschliche Entscheidungsfähigkeiten erweitern. Wir erklären Ihnen die technischen und konzeptionellen Fundamente dieser Schlüsseltechnologie.
Definition zentraler Begriffe
Maschinelles Lernen bezeichnet Algorithmen, die aus Datenmustern lernen – ohne explizite Programmierung. Prädiktive Analytik sagt Fehlerwahrscheinlichkeiten vorher, während neuronale Netze komplexe Zusammenhänge erkennen. Diese Werkzeuge ergänzen klassische Prüfverfahren.
Historischer Kontext und technischer Fortschritt
In den 1980er Jahren dominierten manuelle Stichproben. Heute analysieren Systeme 100% der Produktionsdaten. Ein Meilenstein: 2016 entwickelte ein Automobilkonzern selbstlernende Inspektionssysteme. Resultat: 30% weniger Rückrufaktionen.
Jahr | Entwicklung | Auswirkung |
---|---|---|
1995 | Statistische Prozesskontrolle | Reduktion grober Fehler |
2010 | Cloud-basierte Analysen | Echtzeit-Monitoring |
2023 | Generative Modelle | Proaktive Risikominimierung |
Ein Pharmaunternehmen nutzt seit 2022 Bilderkennung für Verpackungskontrollen. Ergebnis: Fehlerquote sank von 1,2% auf 0,3%. Diese Lösungsansätze zeigen: Technischer Fortschritt schafft neue Qualitätsstandards.
Moderne Anforderungen verlangen adaptive Systeme. Wo früher Einzelparameter genügten, analysieren heutige Tools ganze Wertschöpfungsketten. So entstehen Produkte, die Kriterien von morgen bereits heute erfüllen.
: Voraussetzungen und digitale Transformation
Digitale Transformation beginnt nicht mit Technologie, sondern mit einer Kultur des datengesteuerten Handelns. Unternehmen benötigen eine stabile Datenbasis, um intelligente Systeme erfolgreich einzusetzen. Ohne diese Grundlage bleiben selbst modernste Tools wirkungslos.
Datenqualität und Aufbrechen von Datensilos
Vernetzte Cloud-Systeme lösen veraltete Insellösungen ab. Eine Studie zeigt: 67% der Effizienz-Verluste entstehen durch fragmentierte Datenspeicher. Integrierte Plattformen ermöglichen Echtzeitanalysen über Abteilungsgrenzen hinweg.
Drei Erfolgsfaktoren für maschinelles Lernen:
- Konsistente Datenformate
- Automatisierte Qualitätschecks
- Vernetzung von Produktions- und Logistiksystemen
Datenschutz wird zum strategischen Faktor. Branchen wie die Pharmaindustrie benötigen spezielle Verschlüsselungsstandards. Gleichzeitig steigern einheitliche Datenpools die Vorhersagegenauigkeit um bis zu 40%.
Die Transformation erfordert klare Roadmaps:
- Bestandsaufnahme existierender Systeme
- Priorisierung kritischer Schnittstellen
- Schulungen für datenbasiertes Entscheiden
Unternehmen der verarbeitenden Industrie berichten: Nach der Integration zentraler Datenbanken sinken Fehlerquoten um durchschnittlich 28%. Diese Entwicklung bestätigt: Daten sind der neue Rohstoff des Qualitätsmanagements.
: Methoden der KI im Qualitätswesen
Wie lassen sich verborgene Muster in Produktionsdaten entschlüsseln? Moderne Analyseverfahren kombinieren maschinelles Lernen mit visueller Aufbereitung – ein Gamechanger für präzise Fehlererkennung. Wir zeigen Ihnen konkrete Technologien, die heute branchenübergreifend Erfolge generieren.
Algorithmen für prädiktive Qualitätssicherung
Selbstlernende Systeme identifizieren Abweichungen in Echtzeit. Ein Automobilzulieferer nutzt etwa Entscheidungsbäume, um Schweißnähte zu bewerten. Ergebnis: 45% weniger Nacharbeiten. Generative Modelle simulieren dabei Millionen möglicher Szenarien – von Materialschwankungen bis zu Lieferkettenrisiken.
Drei Schlüsselanwendungen:
- Anomalie-Erkennung durch Deep-Learning-Netze
- Vorhersage von Maschinenausfällen mittels Zeitreihenanalysen
- Automatisierte Prozessoptimierung durch Reinforcement Learning
Visuelle Dateninterpretation in der Praxis
Tools wie Power BI verwandeln Rohdaten in interaktive Dashboards. Ein Pharmahersteller visualisiert damit Produktionsparameter:
Tool | Funktion | Nutzen |
---|---|---|
KNIME | Workflow-Automatisierung | 50% schnellere Fehlerdiagnose |
Tableau | Echtzeit-Monitoring | Reduktion von Stillstandszeiten |
Python-Matplotlib | Statistische Auswertungen | Transparente Trendanalysen |
Diese Lösungen machen komplexe Zusammenhänge auf einen Blick erfassbar. Entscheider erkennen sofort, wo Optimierungsbedarf besteht – ohne IT-Fachwissen. Die Integration in bestehende Systeme gelingt meist binnen weniger Wochen.
Praxisbeispiel: Ein Elektronikhersteller reduzierte durch kombinierte Anwendung von Machine Learning und 3D-Visualisierung seine Ausschussquote um 62%. Die Software zeigt Produktionsabweichungen farbcodiert an – Mitarbeiter reagieren sofort.
: Qualifikation der Mitarbeiter für KI-Einsatz
Sie wissen: Technologie allein reicht nicht. Erst qualifizierte Teams machen digitale Lösungen erfolgreich. Unser Praxisleitfaden zeigt, wie Sie Mitarbeiter systematisch auf neue Aufgaben vorbereiten – ohne Überforderung.
Mindestqualifikationsstufen und Schulungen
Grundlagenwissen in Datenanalyse ist heute Pflicht. Die folgende Tabelle zeigt Anforderungen an Schlüsselpositionen:
Rolle | Schulungen | Praxisaufgaben |
---|---|---|
Qualitätsmanager | Statistik-Grundlagen | Algorithmen-Monitoring |
Produktionsmitarbeiter | Maschinenschnittstellen | Echtzeit-Feedback |
IT-Spezialist | Neuronale Netze | Systemintegration |
Blended-Learning-Konzepte kombinieren Onlinekurse mit Workshops. Ein Automobilzulieferer erreichte so innerhalb von 6 Monaten 92% qualifizierte Belegschaft. Entscheidend: Praktische Übungen an realen Produktionsdaten.
Strategien zur internen Wissensvermittlung
Erfolgreiche Unternehmen setzen auf Mentorenprogramme. Erfahrene Experten coachen Teams bei der Lösung komplexer Fälle. Ein Pharmaunternehmen reduziert so Einarbeitungszeiten um 40%.
Drei bewährte Methoden:
- Gamifizierte Lernplattformen für Basiswissen
- Cross-funktionale Projektteams
- Monatliche “Solution Days” mit Praxis-Challenges
Eine Studie belegt: Betriebe mit strukturierten Schulungsplänen erreichen 3x schneller ROI bei Technologieprojekten. Ihr Vorteil: Mitarbeiter werden zu aktiven Gestaltern – nicht nur Anwendern.
: Optimierung der Qualitätsprozesse im Unternehmen
Effizienzsteigerung beginnt dort, wo Technologie und bestehende Systeme symbiotisch zusammenwirken. Intelligente Lösungen fügen sich nahtlos in etablierte Abläufe ein – ohne Brüche oder Produktionsunterbrechungen. Diese Integration schafft messbare Mehrwerte: 83% der produzierenden Unternehmen verzeichnen laut McKinsey-Studie bereits binnen 6 Monaten spürbare Prozessverbesserungen.
Schlüsselstrategien für reibungslose Implementierung
Erfolgreiche Firmen nutzen modular aufgebaute Systeme. Diese lassen sich schrittweise in kritische Produktionsschritte einbinden. Ein Maschinenbauer integrierte etwa Sensoren in bestehende Anlagen – ohne Umbaukosten. Resultat: 22% weniger Materialverbrauch bei gleicher Output-Qualität.
Prozessschritt | Traditionelle Methode | KI-Integration | Ergebnis |
---|---|---|---|
Fehlererkennung | Stichprobenkontrollen | Echtzeit-Monitoring | +37% Fehlerfrüherkennung |
Ressourcenplanung | Manuelle Kalkulation | Predictive Analytics | 19% Kosteneinsparung |
Wartungszyklen | Festes Intervall | Zustandsbasierte Steuerung | 45% längere Maschinenlaufzeiten |
Drei Erfolgsfaktoren machen den Unterschied:
- Kombination aus Cloud-Lösungen und Edge Computing
- Agile Pilotprojekte mit klarem ROI-Fokus
- Kontinuierliches Feedback zwischen IT und Produktion
Ein Elektronikhersteller zeigt, wie’s geht: Durch automatisiertes Prozess-Mapping identifizierte das Team 12 redundante Arbeitsschritte. Die Verbesserung setzte 560 Personenstunden pro Monat frei – für strategische Aufgaben. So wird Technologie zum Wertmultiplikator statt zum Kostenfaktor.
Handlungsimpuls: Starten Sie mit einer Prozessaudit-Analyse. Identifizieren Sie drei Hebelpunkte, wo Datenanalyse sofortige Ressourcen-Freisetzung ermöglicht. Nutzen Sie vorhandene Infrastruktur – Revolutionen gelingen oft durch Evolution.
: Praktische Anwendungsbeispiele und Pilotprojekte
Wie sieht der Erfolg digitaler Lösungen im realen Produktionsalltag aus? Wir zeigen Ihnen inspirierende Beispiele, die den Weg von der Testphase zur skalierbaren Lösung nachzeichnen. Diese Projekte beweisen: Schon kleine Pilotinitiativen generieren messbare Wettbewerbsvorteile.
Erfolgsstories aus der Praxis
Ein führender Medizingerätehersteller startete 2023 ein Pilotprojekt zur automatisierten Oberflächenkontrolle. Sensoren erfassen dabei Mikrometer-genaue Abweichungen. Ergebnis: Die Fehlerquote sank um 58%, während die Prüfgeschwindigkeit um das 7-Fache stieg. Gleichzeitig lernt das System kontinuierlich aus neuen Daten – es erkennt nun auch Materialermüdungserscheinungen.
In der Lebensmittelbranche optimierte ein Unternehmen seine Verpackungslinien durch intelligente Software. Das System analysiert Füllmengen in Echtzeit und korrigiert Abweichungen automatisch. Dies spart jährlich 240 Tonnen Rohmaterial ein. Die Investition amortisierte sich bereits nach 11 Monaten.
Iterative Vorgehensweisen und kontinuierlicher Mehrwert
Ein Automobilzulieferer demonstriert die Kraft schrittweiser Optimierung. Phase 1 begann mit einfachen Analysen von Schraubverbindungen. Heute steuert ein lernfähiges System die gesamte Montagelinie. Der schrittweise Ausbau brachte:
- 23% weniger Nacharbeit im ersten Quartal
- Automatisierte Dokumentation aller Qualitätsparameter
- Vorhersage von Lieferkettenrisiken mit 89% Trefferquote
Diese Lösungen zeigen: Starten Sie mit klar definierten Teilbereichen. Sammeln Sie Erfahrungen, bevor Sie das System auf komplexere Aufgaben ausweiten. So minimieren Sie Risiken und maximieren den Nutzen.
Ihr nächster Schritt: Identifizieren Sie einen Prozess mit hohem Datenaufkommen. Starten Sie innerhalb von 6 Wochen einen Machbarkeitstest – wir unterstützen Sie bei der Umsetzung.
: Fazit
Die Zukunft der Qualitätssicherung ist kein Zufall, sondern Ergebnis strategischer Entscheidungen. Moderne Technologien verbinden präzise Datenanalyse mit menschlicher Expertise – ein Erfolgsmodell, das Fehlerquoten drastisch reduziert und Ressourcen effizient einsetzt.
Unternehmen stehen vor der Wahl: Verharren in manuellen Routinen oder aktiv Prozessoptimierung gestalten. Studien belegen: Betriebe mit integrierten Lösungen der künstlichen Intelligenz erreichen bis zu 40% höhere Produktivität. Der Schlüssel liegt in der Kombination aus lernfähigen Systemen und qualifizierten Teams.
Zukünftige Entwicklungen werden selbstlernende Algorithmen weiter verfeinern. Prädiktive Analysen antizipieren Lieferkettenrisiken, während adaptive Modelle Produktionsparameter in Echtzeit anpassen. Diese Fortschritte machen Qualitätsmanagement zum strategischen Wettbewerbsvorteil.
Starten Sie jetzt mit konkreten Schritten: Nutzen Sie die vorgestellten Methoden als Roadmap. Initiieren Sie Pilotprojekte, die messbare Erfolge in zwölf Wochen liefern. Wir begleiten Sie bei der Transformation – von der ersten Analyse bis zur skalierbaren Lösung.